Working Group Product Simulation
The WG (working group) product simulation aims on enhancing the finite element method (Subproject 7), the structural optimization (Subproject 9) and the validation of simulations by means of optical scan data (Subproject 10) and integrating them into the knowledge-based framework.
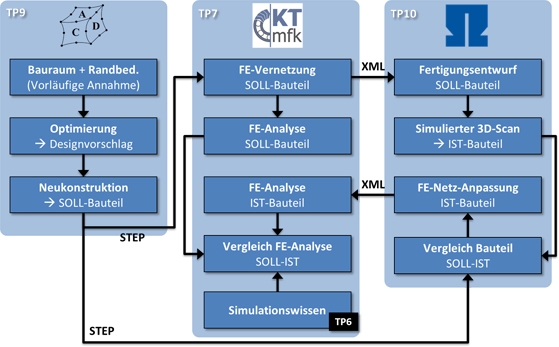
The WG product simulation persists of the subprojects SP 7, SP 9 and SP 10. These subprojects deal with simulative strength and stiffness analyses of mechanical parts. Finite element method, computational fluid dynamics, multibody analysis and structural optimization are the most often used product simulations. During the preparation of a simulation, the problem must be analyzed and a suitable abstraction must be determined. This step is called modeling. Throughout the systems analysis, the simulation task is dissected to clarify its core. Here the top-down or the bottom-up principle can be used, at which meaningful relationships for analysis or synthesis directions are applied. In the WG product simulation these principles are used in combination. On the one hand, it is necessary to understand the whole system like it is achieved through the top-down method (SP 7, SP 9). On the other hand, the bottom-up method with fast running simulations combined with the comparison of prototypes is capable of producing knowledge rapidly. The execution of the simulation is performed in direct dependency to the targets which are defined before. If the aim of the simulation is to optimize a task it could be necessary to run the simulation several times with modified initial values. The systematic variation of the simulation parameters is depending on the operator’s know-how but it is also possible to use mathematical optimization methods. Both approaches are utilized in the WG product simulation. A knowledge-based error assistant (FEA assistant system) to interpret the results of the analysis is engineered in subproject 7, while subproject 9 studies the capabilities of mathematical optimization methods and their usage for the considered production techniques. With this manufacturing-specific structural optimization it is possible to optimize the part for a particular case of application if the load spectrum is known. The mentioned subprojects are dealing with the planning and the understanding of the existing simulation system. The third subproject (SP 10) within WG product simulation is integrating existent manufacturing offsets (e. g. sheet metal spring-back and casting distortion) into the simulation model by scanning part prototypes. The simulation module ‘3D-surface detection’ uses the comparison of the optical determined real data to the ideal geometry from the virtual product development to generate a corrected and simulation-qualified volume model under inclusion of sought-after decision criteria. The WG is using the knowledge collected by the WG knowledge management to configure the models for structural optimization and FEA. The WG process simulation generates rules for process-suitable optimization algorithms and provides simulation data to compare with the scan data.